Sixth, thinner
The role of the diluent has two points, one is to reduce the viscosity of the ink. The second is to thin the ink, thereby increasing the flow properties.
If the ink is thick and sticky, it can be solved with a thinner. For thin and sticky inks, it is better to use a sticking agent.
In fact, the long-term use of No. 6 varnish in the printing industry is itself a dilution effect.
Diluents are liquid solvents. The diluents used in glues and printing inks are mostly ink oils, paraffin hydrocarbons and mineral oils with boiling points around 250-300°C. The diluents used in photogravure printing, overlaying, and roll coating processes are mostly solvents such as benzene, alcohols, esters, and ketones.
Seven, anti-(viscous) dirty agent
Also called anti-fouling agent, in English, in order to distinguish from offset Offset, sometimes anti-fouling agent is represented by Set-offlnkCompound. This refers to the additive that prevents the ink on the print from sticking to the back of another print. Of course, it can also prevent the piles of printed products from sticking together.
Most of these substances are cereal starches, as well as some natural suspended substances. Silica has also been widely used.
These powders can also be added to the ink and dispersed finely. However, the hydrophilicity of starch and its incompatibility with oils can greatly reduce the printing performance of inks, tend to pile up, or pile up on blankets on rollers and printing plates. Filling mesh holes and other ills, it should pay attention.
Most of the printing industry adopts spray process to solve the disadvantages of scumming. For example, after printing, (1) dusting (starch, precipitated calcium carbonate, calcite formed by the reaction of calcium nitrate and ammonium carbonate, fine-grained wax, silica Etc.) The requirements for these powders are fine—generally between about 15 and 40 microns, with low hygroscopicity, neutrality, and no friction, and cannot affect the next process of printing, covering, etc., (2) spraying liquids. , spray the so-called fast-setting vehicle (Fast-Setting Vehicle), this kind of material is composed of one phase is a solid, the other phase is a liquid, printed on the paper, immediately absorbed by the paper selectively, the solvent part immediately and sticky The components are related to each other and form antifouling properties together with the pigment. The composition of such liquids is numerous. Disadvantages of spray-type anti-fouling agents are that they tend to contaminate the air and the machine, causing the operator to feel uncomfortable, and they do not adapt to some advanced glossy paper because it can damage the gloss of these papers.
In recent years, although the ink industry has developed a number of fast-setting inks, the problem of blemishes on printed products has not yet been resolved in a relatively broad range. Therefore, the anti-fouling agent is still in use, and its research is still underway.
The principle behind the development of the anti-fouling aids is that they are composed of immiscible materials. After printing, the additives can float on the surface of the ink layer to form an irreversible “cushionâ€, thereby reducing the offset of the printed products. .
When the additive is added to the ink, the amount is 2-5%, the effect is better.
Eight, defoamer
Defoamers are mainly used for the comparison of dilute inks. Most of these inks can be transported by pumps. During this process, a large amount of air may be mixed in and air bubbles appear. In addition, during the printing process, when these thin inks are scraped off the plate (such as photogravure) or flowed down from the roller (such as a flexographic plate), a large number of bubbles are generated due to the impact and agitation between the inks.
Aromatic, alcohol, and water inks all have this phenomenon, and the latter is the most serious because the latter is mostly an alkali-soluble substance. It is like a soap (or detergent) in water, so it is very foamy. .
The ink bubble not only degrades the quality of the printed product, but also causes a large amount of bubbles in the ink fountain in severe cases, and even the printing cannot be continued.
(a), the brief mechanism of foam formation and destruction
Bubbles, which are formed by the separation of gas into a group of liquid membrane walls. The bubble wall itself can form a very consistent geometry. When the three bubble walls (films) meet together, they form a 120 degree angle. At least two or more components can form bubbles (pure liquids do not foam) because foams require a large amount of surface area to form, and these surface areas are created in opposition to the surface tension of the liquid. Therefore, when the surface tension of the liquid is relatively low, the energy required for forming a certain amount of stable bubbles is also relatively low.
When a monomolecular film of a surfactant that is soluble in a liquid appears on the surface of the liquid, air bubbles are generated. The elasticity of the liquid surface also causes bubbles.
In general, the bubble itself is unstable, and its destruction generally occurs because the liquid squeezes from the wall of the bubble into the edge of the wall. When the film wall is squeezed to a thickness of about 100 Ao, the molecular motion inside the film wall is to destroy. The liquid membrane destroys the bubble structure.
(B), the function of defoamer
The function of defoamers is generally through their chemical reaction to eliminate bubbles (such as acid or calcium salts can destroy the soap film). However, the function of most defoamers is to spread out on the surface of the foam, so that it is removed or replaced before the surfactant stabilizes the air bubbles. This requires more than the surface tension of the original foamed film. Small surface tension. If the foaming agent is easily desorbed and quickly reprocessed, its action against the antifoaming agent is very small. If the desorption function of the foam is poor and the surface viscosity is relatively high, the spread of the antifoaming agent will be slow.
A good defoamer should work quickly. Generally speaking, it should have only a very low solubility in a certain volume of liquid, and it has a very obvious function of reducing the surface tension of the liquid. The chemical structure of the most effective defoamer should be such that it can flatten out when it is oriented at the interface of the bubble. In an aqueous system, this rearrangement is either promoted by the branches of the chain or with the diffusion of bulk polar groups in the center, and is formed by the incorporation of just enough methylene to be water insoluble.
In order to assist the defoamer to have the best diffusion and distribution in the beginning, most industrial defoamers use spreading solvents or emulsifiers as carriers, which can ensure that the defoamer can spread well to the surface. Each part plays an effective defoaming function.
Another method is to add a good solvent to the system so that the surfactant is dispersed in the liquid, so that the formation of bubbles can be greatly reduced.
(c) Classification of defoamers
In general, defoamers can be divided into seven types:
1. Alcohols (2-Ethylhexano!, Polyalkylene Glycols). Branched alcohols and polyols can meet the need for less water solubility and lower surface tension. These two points are the main characteristics that a good defoamer should have.
2. Fatty acids and their derived esters (Sorbitan Trioleate, Diglycol Stearate). Some water-soluble fatty acids and fatty acid esters are mostly used as defoamers in foods.
3. Amides (ethylenediamine Distearoylethylenediamine). This type of defoamer generally has a medium to high molecular weight.
4. Phosphates (TrioctylPhosphate, TributylPhosPhate, SodiumOctylPhosphate). Most phosphate esters are very good at very small amounts.
5. Metal soap (Calcium stearate, Calcium Stearate, Magnesium Palmitate). Pre-dispersion of water-insoluble metal soaps in appropriate continuous mixes can sometimes have effects on non-aqueous systems.
6. Polypolar group-like chemical crystals (Ditertiaryamylphenoxyethanol). Many effective defoamers generally contain two or more polar groups. Castor oil is a natural antifoam containing hydroxyl and ester groups.
7, silicone oils (polysiloxanes - Poiysilonanes). Such defoamers are defoamers that have significant effects on both aqueous and non-aqueous systems.
Silicones are formed by a series of chemical reactions between powdered silicon and some organic chemicals. The silicon-carbon bond structure of silicone is very rare, and the viscosity of silicone oil is x. y. Value related.
Silicone has properties not obtained by other materials. It retains both inorganic and organic properties.
The surface tension of a silicone oil liquid is very low because it contains silicon. The surface tension of dimethyl silicone oil is only about 20 dynes/cm, while the hydrocarbon oil is 35 dynes/cm and the water is 72.8 dynes/cm. Its parts per million can act as a defoamer.
The following system has a good defoaming effect on water-based inks: After trimethylsilyl oil is chain-blocked, it is adjusted to a specific gravity of 1 with an aliphatic hydrocarbon such as gasoline. Double the water and 6% emulsifier (such as Tween 80, Tween is a trade name of surfactant, it is synthesized by Span-Span and ethylene oxide. Span is also a A trade name of a surfactant, which is an ester synthesized from sorbitan and various fatty acids, Tween 80 is synthesized from Span 80 and ethylene oxide, Span 80 is sorbitan monooleate. Ester) is stirred at a high speed and sufficiently emulsified and dispersed.
For aromatic flexographic inks and gravure inks, silicones, especially polymethyl silicones, are more effective. Silicone is less adaptable to alcohol inks.
2-ethylhexanol is a better defoamer for alcohol inks.
Defoamers for the ink industry, silicone oil systems are dominating.
In general, the defoamer is added when the ink is manufactured, and the effect is better than when the ink is used during printing. The latter method can easily cause spots and other defects on the printed product.
For the working population, sedentary is a common normal, all kinds of lumbar disease, cervical spondylosis "into" people's body, bring a lot of trouble to people. Sitting for more than 2 hours without standing up and changing sitting posture is considered as sedentary.
Stand up desk is of great help to healthy office, and modern people's demand for health is also growing. Fully stand in the perspective of users to think about the problem, and the lifting desk with freely adjustable height can bring users a new experience of healthy office.
stand up desk can adjust the height of the desk according to its own needs, so that it can work in the most comfortable state.
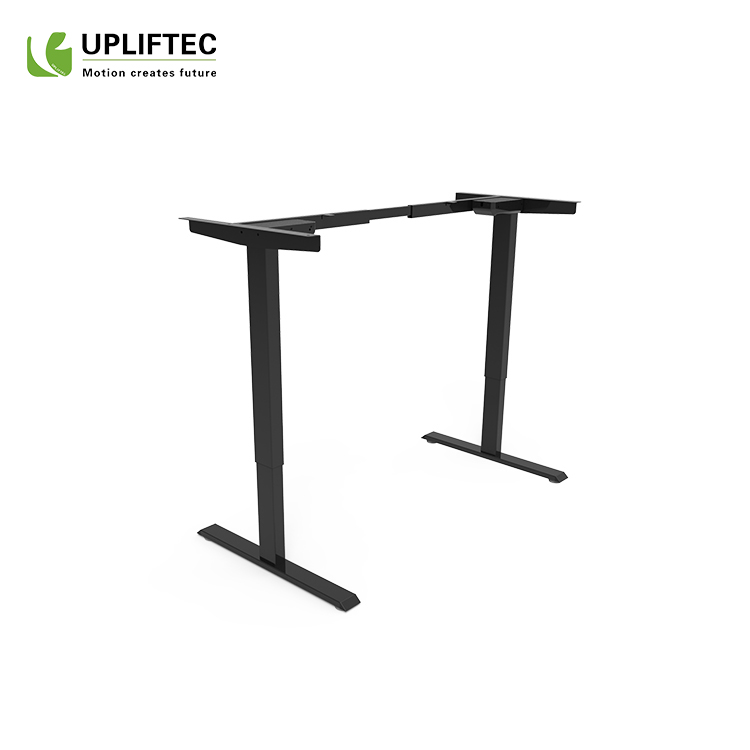
Stand Up Desk,Motorized Standing Desk,Stand Up Computer Desk,Ergonomic Stand Up Desk,Adjustable Desk
Suzhou Uplift Intelligent Technology Co., Ltd , http://www.uplifting-desk.com