Sponge rubber strip is a kind of material commonly used in die-cutting production. Its main function is to help separate the paper from the die-cutting knife, avoiding the problem of loose paper and chaos paper caused by insufficient separation of the paper knife during high-speed die cutting, and can effectively eliminate Paper burrs. Here, the author only talks about the superficial experience of the sponge strip in the process of die cutting and embossing (cold pressing process), so as to throw bricks and jade.
Balance die cutting pressure with 75 degree white arched strip
In the die-cutting process, due to the influence of equipment pressure accuracy, die-cut layout and thickness, and the accuracy of the base template, the overall die-cutting pressure will inevitably be unbalanced. In the die-cutting production of cigarette packets, the shape of the "tongue" side is complicated and the steel knife is dense, while the shape of the "dovetail" side is simple and the distribution of the steel knife is relatively loose, which is limited by the shape and layout of the cigarette pack, and the pressure distribution of the knife die plate is limited. Inevitably unbalanced, the specific performance is that when the paper on the side of the "tongue" has just been pressed out, the paper on the side of the "dovetail" has been completely cut through. If the initial pressure of the bottom is taken with the dovetail knife as the reference, the whole bottoming process is longer, which affects the loading efficiency; if the initial pressure of the bottom is taken with the tongue knife as the reference, the pressure of the dovetail knife is too large and damaged. In a short period of time, there will be serious paper burrs in the dovetail edge, which will even directly affect the service life of the die-cut steel bottom plate.
In response to this phenomenon, the approach we take is to first add two long strips of 75-degree white arched strips (shown in Figure 1) side by side on the side of the dovetail knife. High-hardness, high-elasticity arch strips share part of the pressure on one side of the dovetail knife. The results of many years of practice prove that this method can greatly shorten the time for die-cutting and filling the bottom of the die-cutting plate, and extend the service life of the dovetail knife and the die-cut steel plate. The paper edge problem of the dovetail edge is also relieved to some extent. . In addition, in the vicinity of a local steel knife with sufficient position, the method of sticking the strip can also be used to adjust the local knife pressure.
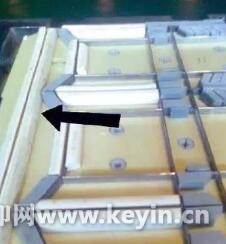
As far as the actual use is concerned, the white arched strip glued on the wooden board can be used continuously until the die is scrapped; if it is pasted on the steel plate, the mold should be inspected when the number of die-cut products reaches half of the approved number of prints. The flatness of the cutting pressure to determine if a new 75 degree white arched strip needs to be replaced.
Quickly align the embossed position with a sponge strip when the paper is deformed
Experienced cigarette packs should be known to people: paper stretch deformation is everywhere. The environmental humidity has changed greatly, the printing tension and temperature have changed, and the product processes have been increased. The semi-finished products have been screen-dried or air-dried, and the die-cutting and convex products have been placed for a long time... These factors have almost become paper. Telescopic deformation of the "signal bomb". For the cigarette-pressing convex parts, more than 90% of them will have a fixed registration position, and the registration requirements are quite strict, and the standard error is ≤0.3mm. If the whole batch of products has regular paper stretching and deformation, it is better to waste a lot of time and re-adjust the position of the pressing plate in a painstaking manner; but if it is intermittent paper stretching deformation? Just corrected the position of all the embossed plates for a few minutes, but suddenly found that the paper size has changed back, it is really crazy!
Want to say goodbye to the dilemma and never-ending revision? A sponge strip can solve the problem. If you don't want to change the position of the embossed plate, then let's change the position of the paper. As shown in Fig. 2, a sponge strip is glued between the two embossed bottom plates, which artificially shrinks the paper in the middle, and then adjusts the normal moment position, and it takes only a few minutes to register the embossing position. If the paper changes back to its original size, immediately stop the sponge strip and everything will return to normal. This method is also applicable to the problem of partial embossing registration misalignment on the periphery of the paper.
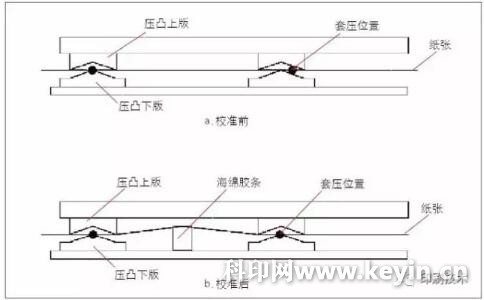
One of the most serious paper deformations I have experienced has occurred in the production of a "soft-pack hardened" cigarette pack. The cigarette pack adopts the process of " offset -screen printing-embossing", a single sheet of 16 spells, a total of 48 embossing, and the embossed Chinese character strokes are extremely thin, the embossed graphic is a light column laser silver material, and the background color is dark red. The contrast is very clear. The author found that the paper size after printing has a contraction of 0.3mm in the direction of the side gauge, the original size, and the expansion of 0.2mm. The average paper stretch will change every half hour or so. According to the conventional method, the position of the embossing plate can only be adjusted for the paper size which accounts for the largest proportion, and the products of the other two paper sizes are sacrificed, and the embossing rejection rate is estimated to be more than 20%. After taking over this product, the author first changed more than 30 embossed plates, adjusted the embossing plate to a position suitable for registering 0.3mm paper, and prepared two sets of sponge tapes with different hardnesses of 25 degrees, and then kept on. No intermittent sampling: When producing the original size paper, paste the low-temperature sponge strip at the intermittent position of the embossed bottom plate; when the paper is enlarged to 0.2mm, replace it with a higher sponge strip; Remove the sponge strip when the paper is mm. The final inspection results show that: a work order is produced, the compacted scrap rate is only 4 percentage points higher than the approved scrap rate, and the timely delivery of the product is ensured because the frequent adjustment work is avoided.
DONG GUAN CITY CHING XIN INDUSTRIAL CO LTD , https://www.chingxin.com