(This article is an original article from Bisheng. It is forbidden to reprint, and reprinting must be corrected)
Three common molding failures and troubleshooting methods
Die-cutting indentation to produce qualified products should have accurate cutting position, clean cut, no burrs, flower knife, clear indentation, and moderate depth.
Common faults and solutions in die cutting and indentation operations:
â‘ The indentation is not clear, there are dark lines, and the lines are exploded. (The dark line refers to the undesirable indentation; the explosion line refers to the cardboard breaking due to the excessive pressure of the indentation)
Causes: Poor paper quality, too low water content of the paper, increasing its brittleness and decreasing toughness; wrong choice of steel wire; steel wire pad paper is too low or too high; improper pressure adjustment of the molding machine.
Solution: readjust the height of the steel wire; check whether the steel wire is suitable; adjust the pressure of the die-cutting machine appropriately; adjust the process conditions of the die-cutting indentation according to the condition of the molded cardboard to make the two fit as much as possible.
â‘¡ The incision is not smooth.
Causes: The steel knife is of poor quality, the cutting edge is not sharp, and the die cutting is not suitable; the cutting is not timely, the cutting edge is seriously worn; the pressure of the die cutting machine is low or the pressure adjustment is not coordinated with the height adjustment of the steel knife, and the die cutting operation is not compact .
Solution: Regularly check the wear of the blade of the steel blade, and change the steel blade in time; choose steel blades with different quality characteristics according to the cutting performance of the paper used in the printed matter; increase the pressure appropriately; readjust or replace the steel blade or pad paper, so that Obtain a solid pressure effect during die cutting.
â‘¢ The position of die-cutting indentation is not correct.
Causes: The position of the arranging knife does not match the printed product; the position of the paper feed in the die-cutting operation is inconsistent; the cardboard gripping rules are inaccurate; the cardboard is deformed and the overprint is not accurate during the operation.
Solution: According to the requirements of the proofs, re-correct the position of the printing plate; adjust the positioning rules of the die-cut paper feed to make it consistent with the position of the paper feed; reduce the impact of print defects on the quality of the die-cut according to the cause of the position.
â‘£ The indentation line is irregular.
Causes: The tightness of the row knife and the fixed knife is not suitable, and the bottom cannot reach the ideal contact effect with the iron table plane. Twisting is easy to occur during the indentation (the steel wire is too tight); ); The thickness of the steel wire pad paper is insufficient; the groove angle is not standardized, and there are extra rounded corners; the indentation groove on the steel wire pad paper is left too wide, and the position is not fixed during the indentation.
Solution: replace the steel wire pad paper, leave the pressure groove narrow; increase the thickness of the steel wire pad paper; correct the groove angle; the knife tightness should be appropriate.
⑤ After die cutting, there is a continuous knife on the cardboard.
Causes: The pressure on the template is uneven, and the knife is connected where the pressure is low; the blade of the die is not sharp, which causes the knife; the paper is too thick to cut through the paper completely.
Solution: replace the die knife according to the actual situation; increase the local pressure.
â‘¥ After die cutting, the cardboard sticks to the knife plate.
Causes: The rubber stuffed around the knife line is too sparse, and the resilience is insufficient; it is not appropriate to choose according to the performance of the rubber; the steel knife is not sharp, the paper is too thick, causing the clamping knife or excessive pressure.
Solution: According to the situation of the plate steel knife, choose rubbers of different hardness reasonably, and when clogged, pay attention to the distribution of the dense and dense distribution, the main knife edge should not be omitted; adjust the pressure appropriately to make up for the lack of sharpness of the blade, if it cannot be solved The problem is to replace the steel knife in time.
⑦ Folded cardboard crease crack.
Cause: If the outer side of the cardboard indentation is cracked, the indentation is too deep or the width of the indentation is not enough; the internal cracking of the cardboard; the molding pressure is too large or the crease is too deep.
Solution: appropriately reduce the height of the steel wire, and widen the indentation line appropriately according to the thickness of the cardboard; reduce the die cutting pressure or replace the slightly lower steel wire.
â‘§ The solution of paper deformation die-cut version:
Due to the influence of objective factors, the printed paper is deformed to varying degrees, which causes the die cutting position to be incorrect and re-make the die cutting plate, which causes great difficulty for post-processing die cutting and forming , Greatly reducing the qualified rate of finished products.
The double-knife die-cutting position can be added at an appropriate position in the deformation direction of the printed product to form a front-rear or left-right separation unit. An adjuster is installed between the double-knife die-cutting positions to adjust according to the deformation direction of the printed product during die cutting. According to the deformation size of the printed paper, adjust it at the adjustment position of the hex screw of the adjuster. The square increases the distance between the double knives and the reverse decreases the distance between the double knives. The maximum adjustable distance is three millimeters.
Four operation rules of die cutting machine
★ Operating procedures before starting
(1) Check the handover record to understand the operation of the equipment
(2) Check the quantity of die-cutting and product quality according to the production construction order requirements according to the production scheduling plan.
(3) After checking and confirming that there are no foreign objects on the machine, thoroughly inspect and adjust the machine.
★ Operating specifications before starting production
â‘ Check whether the die cutting is the same size as the box sample
â‘¡ Check if the product has a mouth
â‘¢ Select the bottom template material according to the number of products, paper type and carton structure
â‘£ Install the die-cut plate, and fasten the screws to prevent the die-cut plate from loosening. Make the bottom template, the thickness of the bottom mold is the thickness of the paper of the die-cut product
⑤ Install the bottom template, clean the surface debris and lock
â‘¥ Adjust the die-cutting pressure according to the thickness of the paper. The pressure should be gradually increased from light to heavy to 80% penetration during adjustment, otherwise it will cause equipment damage
⑦ Adjust the position of the top and bottom thimble of the unloading part and lock it
â‘§ After adjusting each part, produce samples according to the box sample requirements, check that there is no quality problem, and the normal production can be produced after the supervisor signs the sample.
★ Operational specifications in production
(1) Operate in accordance with the production requirements and signing standards of the construction order.
(2) During the production process, samples are inspected every 5-10 minutes, and quality problems are reported in time, and production can be continued after being resolved.
(3) After each version of die-cutting, a comprehensive inspection shall be carried out and the "die-cutting process sheet" shall be filled out. If there are quality problems, the products should be placed separately in time, and fill in the "Abnormal Product Process Sheet".
(Iv) If a material problem is found, the production should be stopped, and the "Feedback Form for Poor Quality of Production Materials" should be filled out to allow relevant departments to coordinate and solve the problem and prepare for subsequent production.
★ Operational specifications after production
(1) The captain should fill in the "Daily Cut Daily Report", "Statistical Table of Process Quality Status" and "Daily Inspection Form of Production Equipment" every day.
(2) Place the die-cut products separately as qualified products and defective products, and mark them clearly.
(3) At the end of production, the equipment should be stopped at the mold opening location.
(Iv) Maintain equipment according to daily maintenance content.
(V) Fill in the handover record carefully.
(Vi) Turn off the power.
Five die cutting and creasing equipment
According to the different shapes of the main working parts of the die-cutting plate and the press-cutting mechanism, the die-cutting machine can be divided into three types: flat press, round press, and round press round; Different directions and positions can be divided into vertical and horizontal.
â–² Flat die cutting machine
When working, the platen table is fixed, and the pressure plate is pressed against the platen plate by transmission to press the platen plate.
The vertical flat pressing and cutting machine has the advantages of simple structure, convenient maintenance, easy to master the operation and replacement of the cutting and indentation plate, etc., but the labor intensity is large and the production efficiency is low. For small batch production.
The platen and platen working surface of the horizontal flat press die press are in a horizontal position, and the platen below is driven by the mechanism to press up against the platen to feel the indentation. Because the stroke of the horizontal molding machine is relatively small, it is difficult to manually insert or remove the cardboard, usually with an automatic paper feeding device.
â–² Round flat die cutting machine
The die-cut version is embedded on the reciprocating platform and comes into reciprocating contact with the impression cylinder. Because the round flat die press uses a cylindrical pressure roller instead of the pressure plate, the die cutting is not "surface contact" but "line contact", which makes the machine bear less pressure during molding, and It is evenly distributed over a long period of time, so the load of the machine is relatively stable and large-format die cutting can be performed.
â–² Round die cutting machine
The round die-cutting machine uses one or more sets of die-cutting rollers to carry out precise, continuous, high-speed rotation of die-cutting indentation and embossing on web printing. Its characteristics: it can run synchronously with the printing line and become a unit in the line, which realizes the one-time completion process of web paper from printing to die cutting to waste edge paper removal; high-precision registration device and die cutting phase high-speed device High die-cutting accuracy; continuous rolling die-cutting, up to 350m / min.
â— Model and performance of common molding machine
model
MPQ1040 automatic scrapping flat die-cutting machine MY820 split rotary platform die-cutting and creasing machine BOBST roll paper stamping and pressing combination machine UNICUTTER5002BAIDU_CLB_singleFillSlot ("205919");



According to news from the US wxow website, screen printing machine manufacturers ... [detailed]
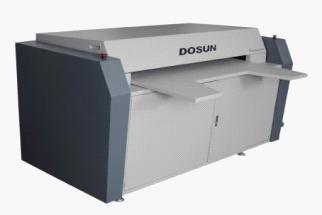
Recently, Hangzhou Dongcheng Image Technology Co., Ltd. hit hard, ... [detailed]

Innovative black and white digital printing system-with a more comprehensive comprehensive ... [detailed]
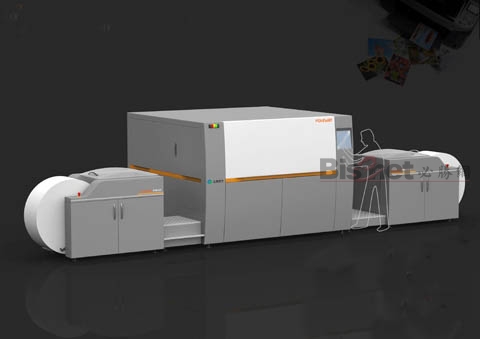
Shanghai Ziguang Machinery Co., Ltd. will be held in November 2011 ... [detailed]
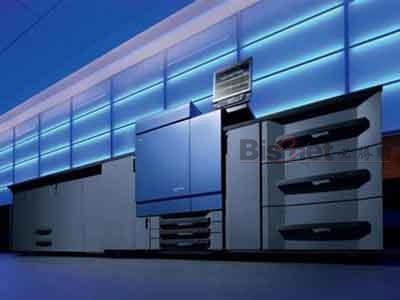
On August 5, 2011, Konica Minolta exhibited it in Beijing ... [detailed]
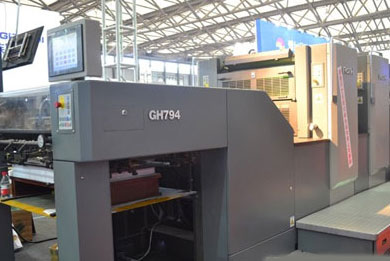
The 4th China (Shanghai) All India Exhibition was grandly held on November 14 ... [detailed]





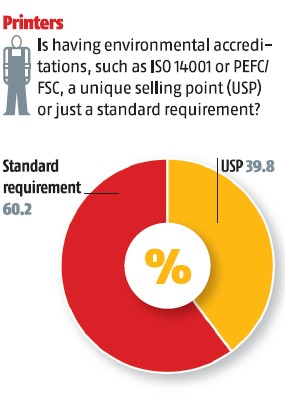
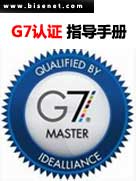

The National Press and Publication Administration recently released "The Basic Situation of the National Press and Publication Industry in 2018 ...

2020-04-13 | Issue 1112: The Ministry of Ecology and Environment has made a big move to resume work!
2020-04-01 | Issue 1111: Printing package colleges to stabilize employment "a big move"!
2020-03-25 | Issue 1110: Why are more and more printing companies aiming at the block
2020-03-17 | Issue 1109: Central government policies support the resumption of manufacturing enterprises
Hair Trimmer,Professional Electric Hair Trimmer,Electric Hair Clippers Tools,Quickly Clean Hair Trimmer
ZHEJIANG SHENGFA ELECTRIC APPLIAMNCES CO.,LTD , https://www.shengfa-appliance.com